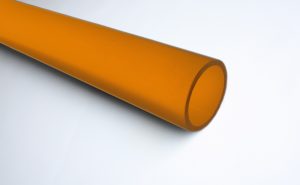
HDPE Cores: A Versatile and Reliable Industrial Solution
High-Density Polyethylene (HDPE) cores have become an optimal solution across various industrial sectors. Their versatility, durability, and lightweight properties make them a perfect choice for demanding applications such as plastic film winding, technical adhesives, and sterile films used in the medical sector.
As an expert in plastic extrusion and co-extrusion, ABI Profils takes a closer look at why HDPE is a key material in the industry and the advantages it brings to plastic cores.
Why Choose HDPE for Your Cores?
High-Density Polyethylene (HDPE) is a thermoplastic polymer highly valued for its outstanding mechanical properties. Produced through the polymerisation of ethylene gas, HDPE has a linear structure that gives it high rigidity and excellent impact resistance, while remaining relatively lightweight. These characteristics make it an ideal material for cores used in intensive industrial applications.
HDPE cores offer several key benefits:
- Lightweight yet strong: Although lightweight, HDPE is robust enough to withstand heavy loads. This makes the cores easy to handle while ensuring long-term durability.
- Chemical resistance: HDPE is highly resistant to a wide range of chemicals, making it ideal for industrial environments exposed to corrosive or aggressive substances.
- Waterproof properties: Due to its non-porous structure, HDPE prevents liquid penetration, ensuring safe use in industries such as food processing and healthcare.
Industrial Adaptability: Custom-Made Cores
One of the greatest strengths of HDPE cores is their adaptability to various industrial configurations. Do you require specific dimensions or enhanced mechanical resistance? At ABI Profils, we can offer customised solutions tailored to your exact project requirements.
Our HDPE cores are available in a wide range of diameters and lengths, with options for smooth or grooved inner finishes. Your final product will be perfectly adapted to your needs.
Industrial Applications of HDPE Cores
HDPE cores are widely used across multiple industries due to their versatility and reliability. Here are some examples of their key applications:
- Food Industry: HDPE cores ensure 100% hygienic conditions for food-grade plastic film winding, while maintaining excellent mechanical resistance.
- Technical Adhesives: The precision offered by HDPE cores allows for tight tolerances and accurate cutting, which is essential for technical adhesive applications.
- Medical Sector: HDPE cores are widely used for sterile film winding. They meet the strict standards of the medical industry thanks to their non-toxicity and resistance to chemicals.
A Sustainable and High-Performance Solution
In addition to their exceptional mechanical properties, HDPE cores represent a durable solution. The longevity of the material, combined with its high resistance to wear and tear, reduces the costs associated with frequent equipment replacement.
Furthermore, HDPE is recyclable, making it a sustainable and environmentally friendly option for industries looking to minimise their ecological footprint.
Conclusion
HDPE cores are a technically reliable and high-performance solution for numerous industries.
They are chosen for their strength, lightweight nature, and remarkable adaptability, meeting the requirements of modern production processes.
At ABI Profils, we work closely with our clients to design custom-made HDPE cores that precisely meet their needs.
To find out more about our HDPE cores and how we can support your projects, contact us today via our online form or call us on +33 (0)4 71 61 29 99.
Back to news home page