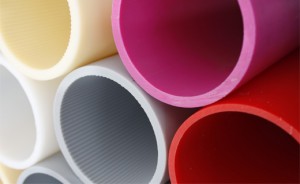
How to Choose the Right PVC Core for Your Industrial Production: 5 Key Criteria
To help you make the right choice, here are the 5 key factors to consider when selecting a high-performance industrial core that is durable and compatible with your production line.
At ABI Profils, we design custom plastic cores tailored to meet the most demanding industrial requirements.
These technical components play a key role in the winding of plastic films, textiles or adhesive materials. A poorly sized or unsuitable core can lead to deformation, slower production speeds, or even damage to your equipment.
To help you make the right choice, here are the 5 key factors to consider when selecting a high-performance industrial core that is durable and compatible with your production line.
1. Selecting the right material for your plastic core
The PVC core is made from polyvinyl chloride, a rigid polymer known for its:
- Excellent chemical resistance
- Outstanding dimensional stability
- Reliable performance in humid environments
It is particularly suitable for use in the packaging, textile and plastic processing industries.
Technical alternatives
Depending on your needs, we also supply plastic cores made from other materials:
- PP (polypropylene): lightweight and heat resistant
- HDPE (high-density polyethylene): robust, ideal for harsh environments
Our experts are here to help you identify the custom core best suited to your application.
2. Core dimensions: accuracy and compatibility
Choosing the right dimensions for a PVC core is essential to ensure compatibility with your winding system and to maintain optimal performance.
- Inner diameter: must match your winding equipment
Various shaft systems are used in winding/unwinding processes. The core’s inner diameter must precisely fit the equipment used on your production line.
Each shaft type has its own technical characteristics:
1. Expanding air shaft
- Principle: The shaft contains air chambers or mechanical segments that expand when air is applied, locking the core or roll in place.
- Applications: Winding/unwinding of plastic films, paper, textiles, metallic foils.
2. Mechanical cam or segment shaft
- Principle: Movable metal segments expand via cams or an eccentric system to grip the core.
- Applications: Suitable for more rigid or heavy materials (metal sheets, large paper rolls).
3. Standard shaft (solid or smooth)
- Principle: A solid shaft on which the roll is mounted and held in place with clamps or collars.
- Applications: For materials where precise locking is not required.
4. Friction shaft (differential shaft)
- Principle: Uses friction sleeves that adjust tension automatically when winding multiple rolls simultaneously.
- Applications: Paper, plastic films, textiles.
5. Conical shaft (or conical expanding shaft)
- Principle: Used for conical cores; the shaft expands progressively for a secure fit.
- Applications: Winding of cables or metal wires.
- Outer diameter: determines load capacity, crush resistance and stability during unwinding
At ABI PROFILS, our teams take these factors into account to offer an efficient, optimised solution. We provide a wide range of standard and custom dimensions adapted to even the most demanding production environments.
3. Inner finish: smooth or grooved?
The internal surface of a plastic core affects handling and the stability of the final product. There are two options:
- Smooth PVC core: ensures uniform, jerk-free unwinding and allows for easier handling.
- Grooved PVC core: ideal when extra grip is needed to stabilise film or textile. Recommended for slippery materials (LDPE films, fine textiles); improves grip and stability
Each finish is suitable for a specific type of film or textile. Our team advises you based on your constraints.
4. Resistance to production environment
The industrial environment directly impacts the longevity of a plastic core:
- In humid or chemical environments, PVC is an excellent choice to prevent corrosion and deformation
- For thermal shocks or high temperatures, PP or HDPE may offer better performance
Every industrial plastic core we manufacture is built to withstand your production environment’s challenges.
5. Profitability, durability and compliance
A high-quality PVC core helps to optimise industrial performance while meeting environmental and regulatory standards.
- Durability: Designed to withstand repeated mechanical stress, our cores offer extended service life and reduce production downtime.
- Recyclability: Depending on your specifications, we offer plastic cores made from regenerated materials – a technical solution that reduces environmental impact without compromising performance.
- Standards compliance: All our industrial cores are manufactured according to current standards. We guarantee high-quality, reliable products that fully meet your technical and regulatory requirements.
At ABI Profils, we combine profitability, quality and environmental responsibility in every custom core we design.
Your custom PVC core with ABI Profils
Choosing the right industrial plastic core depends on a variety of technical and environmental factors. By considering material, dimensions, inner finish, production environment and profitability, you can optimise every winding process.
ABI Profils supports its clients in selecting the PVC core that best matches their needs. Contact our team to discuss your requirements and get personalised support.
Need support? Contact us via our online form or by phone on +33 4 71 61 29 99.
Back to news home page